WHALE SCULPTURE
GLOBALGATE
SASASHIMA-LIVE NAGOYA (2017)

●クジラの骨格標本の制作
グローバルゲートプロジェクトでは、クジラの骨格標本にチャレンジしました。すべての骨を欅(ケヤキ)の無垢材から削り出して作製しています。全長12M×全幅3.5M×高さ2M。
クジラは地球史上最大の生物と言われ、体長34M、体重はなんと190トンにも及ぶシロナガスクジラの記録もあります。
どこまでも続く深く青い海。
時折浮上して見えてくる流線型の巨大な陰影。
私はそんなクジラに、自然環境それ自体のアイコンとなり得るほどの存在感とメッセージ性を感じます。
このクジラという生き物の雄大さ・神秘性、そして「人と自然の共存」というクライアントの企業理念を表現するため、骨のひとつひとつには、実物の再現に加え、シェイプラインによりエッジを利かせ、ライティングとの相乗効果によるハイコントラスト効果を狙いました。これにより、スカルプチュアとして美しさを最大限に引き出すことに成功しています。



クジラの骨格は、大きく分けて4つのパートで構成されています。
・頭蓋骨や下あごの頭部
・私たちで言う腕の部分にあたる胸ビレ部
・あばら部
・頸椎から背骨、尾尻の先まで続く部分
大きいもの3M(300Kg)から、小さなもので約10cm程度のものまで、大小さまざまなこれら156パーツから成り立ちます。
粗出しした156個それぞれのベースブロックに墨出しをして、それをさらに、様々な大きさのチェーンソーを利用してカットしていきます。
作製の道のり
このクジラの作成には、幼馴染でありチームのメンバーである山口材木店、地元の後輩君、森林組合や木こりの方々など、多くの方々の協力を頂きました。
①まずは、材料となるケヤキの丸太を切り出しました。
最大パーツとなる頭部に使う丸太の直径は最大値1.5M、丸太の重量は3tを優に超え、なんとバー長さ1.5Mのチェーンソーでの伐採となりました。そして、製材するにも製材機に入らなかったことから、パーツの粗出しにもバー長さ1Mのものを使用しました。
刃の目立てにも時間がかかるかかる、、、(笑)
真夏の炎天下の下、御年80の伝説のきこりHさん、ありがとうございました。
※ちょっとその前に(その1)
トラックに積み込みの右写真、丸太を玉掛けしているロープが異様に細いことに気が付くでしょうか?
これは、アウマクアで製品開発中の、特殊素材を使った玉掛け用ロープで、6tの重量に耐えることができるものです。
※ちょっとのその前に(その2)
そもそもクジラの骨格がどのような成り立ちをしているのか、その骨格の仕組みや構造を知るために、色々な博物館や水族館に足を運び、骨格標本関連の蔵書などを求めて図書館なども巡りました。
展示されている骨格標本をスケッチし、シェイプラインを頭に叩き込みます。
ここでは、1人では水族館をうろうろできない私のために、山口材木店の山口くんと、彼の美人御嬢にお付き合い頂きました。




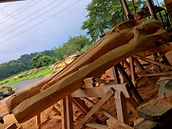

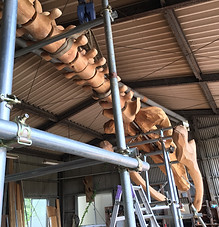
粗出ししたあばら骨と頭蓋骨。頭蓋骨に至っては、この時点で300Kg以上の重量があるため、フォークリフトやユニック車のクレーンを用いて向きを変えながら、カット作業をしていきました。
粗出しの目処がついたら、次はさらに形状をシェイプしていきます。特殊な回転工具に特殊なカッター刃をセットし、徐々に形が定まってくるわけですが、組み上げた時の接合部の整合性を逐一確認しながらの作業となるため、部分的に組み上げながら、シェイプ作業を続けます。
真夏の太陽が照り付ける中、作業の途中途中で、色々な課題や困難が降りかかりました。接合部に過度な重量がかかっていることが判明し、仕上がりかけていたパーツがひび割れて折れたり、接合芯材の位置がずれていて再度パーツを作り直したり、、、
私たちの壮大な夏休みの工作は、たびたび深夜に及びました。
運搬~搬入~設置工事
運搬に際しても、幾つかの大きな問題がいくつもありました。
まずは、仕上がったこのクジラを、傷付けることなく運ばなければならないということ。荷台に放り込めばいいという事ではありませんし、形状も様々で、サイズも重量もあるパーツもあります(下あご長さ2.4M×重さ80㎏、頭部長さ2.6M×重さ180㎏)。
そして、現地での人手、搬入経路と、与えられた搬入時間の問題もありました。こうした現場では、搬入の際に、それぞれに与えられた「持ち時間」というものがあり、その時間内に搬入をこなさなければならないのです。
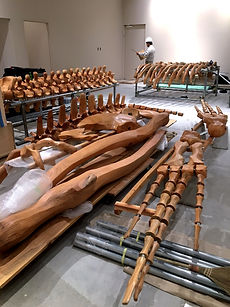

それぞれのパーツを傷付けることなく、効率的な搬入を実現させるために、たちは特注の運搬車を作成し、これらの課題を解決しました(しかも、この運搬車を解体すると、骨格を設置する際の支柱材として利用できるようにしました!)。
こうした搬入現場では毎度のことですが、戦場さながらの様相です。搬入順を待つトラックの長蛇の列、積み下ろし場所の陣取りや、エレベーターの争奪戦、そもそものところ、10t車の積み荷を40分で降ろしなさない、みたいなキャパオーバーなことを言われているので、みんなそれぞれが、1分でも持ち時間を引き延ばそうと必死になり、決められた場所よりも少しでも広く荷下ろし場を確保しようと躍起になり、大声が飛び交い、時には言い争いも起こります(引っ込み思案ではなにもできません、、!)。
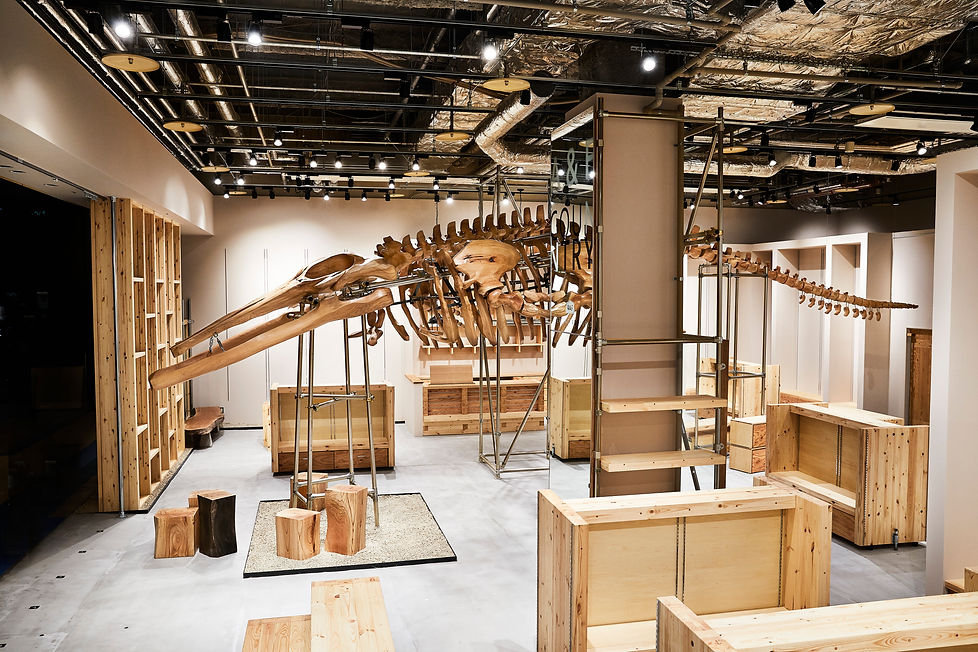
私たちの現場では、常にたくさんの方々が設置作業を見学に来てくれます(それもそのはず、通常の内装業者さんがやらないような、突飛なことをやっていますから)。今回も、内装監理室、グローバルゲート、A,B,C工事に携わる様々な方々が、見学に訪れて下さいました。
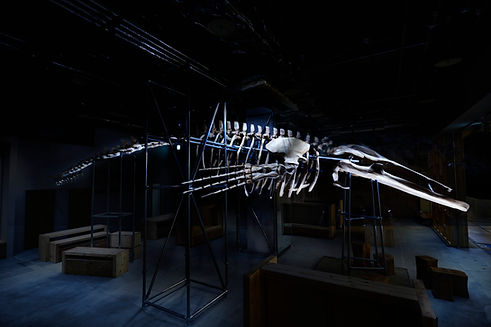

様々な困難を乗り越えて、今回の骨格標本のプロジェクトも無事に終えました。
全ての作業が楽ではなかった今回のプロジェクト。作成作業は約3ヵ月、トータルで25Mプール一杯分ぐらいの木くずにまみれた、壮大な夏休みの工作でした。完成に際しては、株式会社ヴィジョナリーバンガードの若井寛君に撮影を依頼し、素敵な写真を撮って頂きました。ありがとう!!
そして今回も、チームメンバーのみんな、作業に協力して頂いたみなさま。このような機会をくれたA&Fのみなさま。
本当に本当にお疲れさま&ありがとうございました!!
